Wear Monitoring in Pick-and-Place Machines
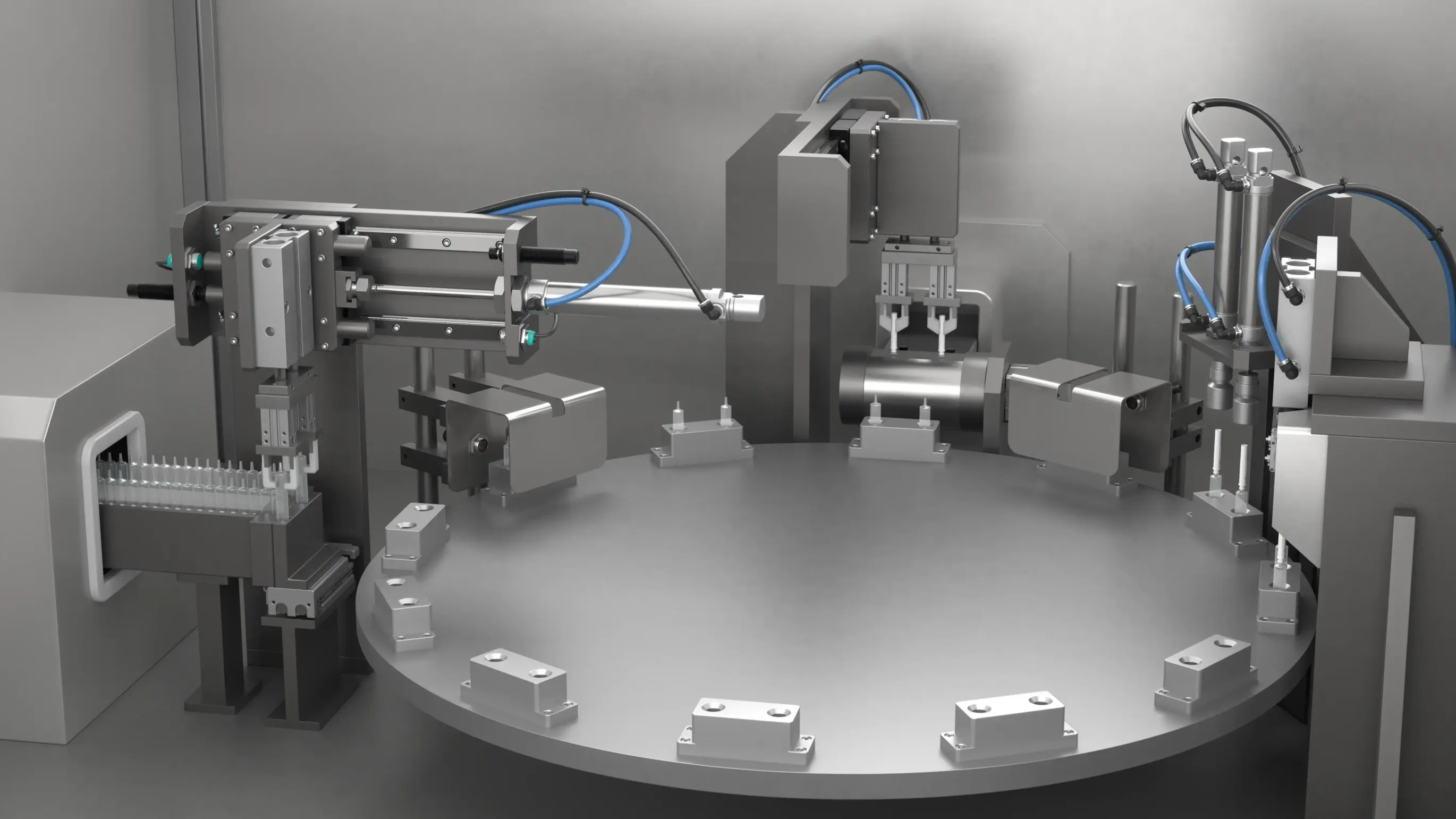
Inductive Distance Sensors with IO-Link for High Object Speed

The Application
In pick-and-place applications, there are numerous actuators that perform a linear movement. Before reaching the end position, this movement is often slowed down by shock absorbers. These dampers are subject to operational wear. In order to maintain the function of the machine, they are replaced before they are worn out. The same applies to other actuating elements such as hydraulic cylinders.
The Goal
The condition of the actuating elements should be continuously monitored, with the current level of wear recorded as accurately as possible. This condition monitoring enables targeted replacement of worn components and allows maintenance activities to be scheduled during planned downtimes.
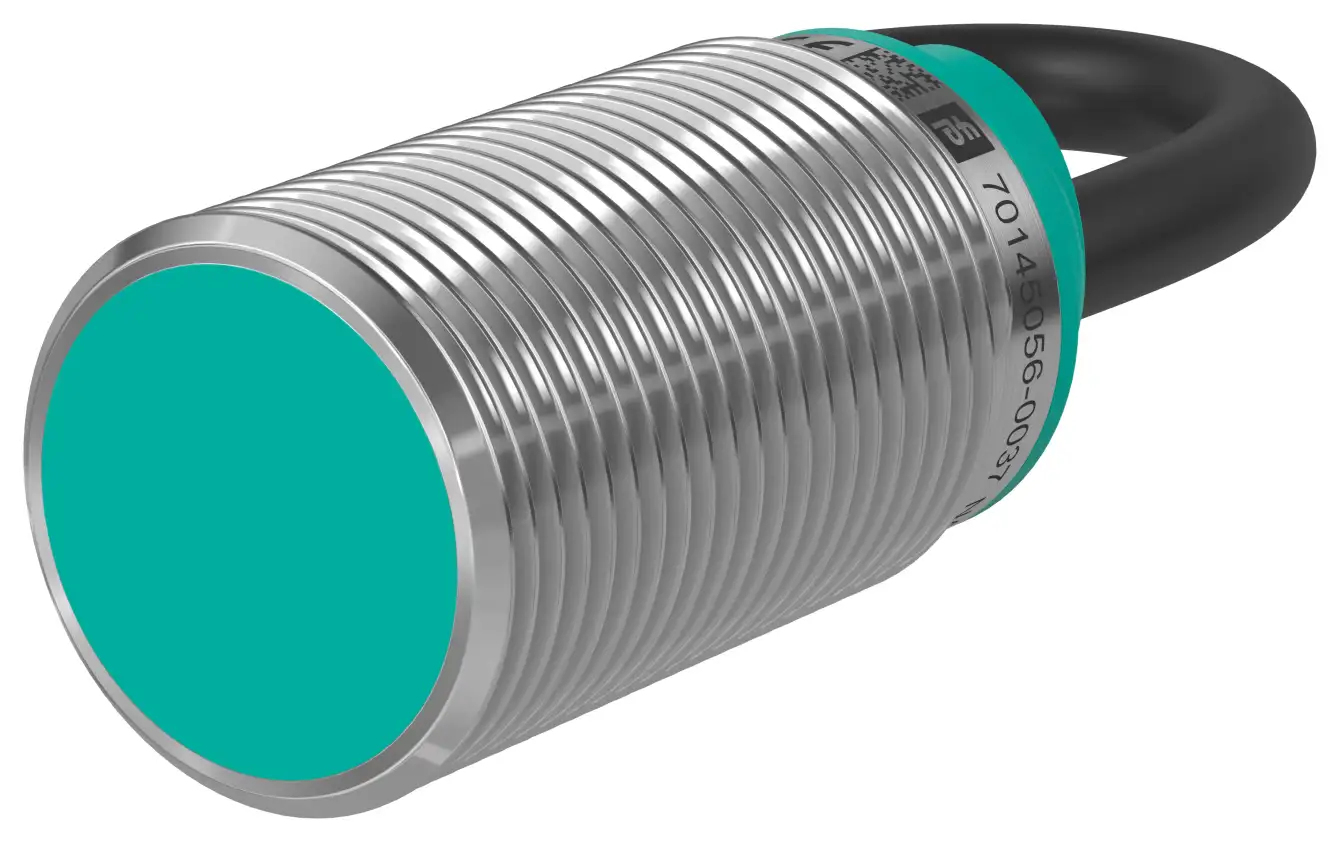
The Solution
The movement of the actuating elements is detected by inductive distance sensors. They measure the speed and determine the acceleration of the target object with high precision, even at very high object speeds of up to 3 m/s. In addition, two measurement windows can be configured in order to obtain an acceleration value for differentiated sequence monitoring.
The sensor carries out two speed measurements for each movement of the actuating element and uses this to calculate the braking effect of a damper, for example, as negative acceleration. The measurement data indicates the degree of wear so that maintenance can be triggered in a targeted manner. The IO-Link interface enables both continuous communication with the control system and the transmission of detailed status information. In addition to data on distance, speed, and acceleration, the sensor also provides the basis for comprehensive condition monitoring and predictive maintenance.
Technical Features
■ Robust noncontact measuring principle
■ Maximum switching distance up to 30 mm
■ Target speed up to 3 m/sec
■ Switching frequency up to 1,400 Hz
■ IO-Link interface
■ Various housing designs
■ Integrated temperature sensors (optional)
The Advantages
Maintenance processes are no longer triggered cyclically, but when they are actually needed. At the same time, they can be planned for the long term and coordinated with other processes in the plant. Long downtimes and unplanned system standstills are thus reliably avoided. The unimpaired function of the dampers and other actuating elements protects other machine components. This increases efficiency and reduces costs.
At a Glance
- Built-in condition monitoring (e.g., speed and acceleration of actuators)
- Supports predictive maintenance for shock absorbers, cylinders, valves, etc.
- Offers detailed data and custom limits via IO-Link (e.g., temperature, run time)
- Fast measurement up to 3 m/s for higher throughput and productivity
- In-house development with market-leading experience and expert support