Position Feedback and Progress Analysis on On/Off Valves

Inductive Distance Sensors with IO-Link Provide Precise Status Data
The Application
Flaps and valves control the flow of liquid and gaseous substances in the process industry. If these are on/off valves, they are moved to defined end positions when opening and closing. The current position of such a valve can be crucial information for controlling the system. Monitoring the valve status also plays an important role with regard to the availability of the system.
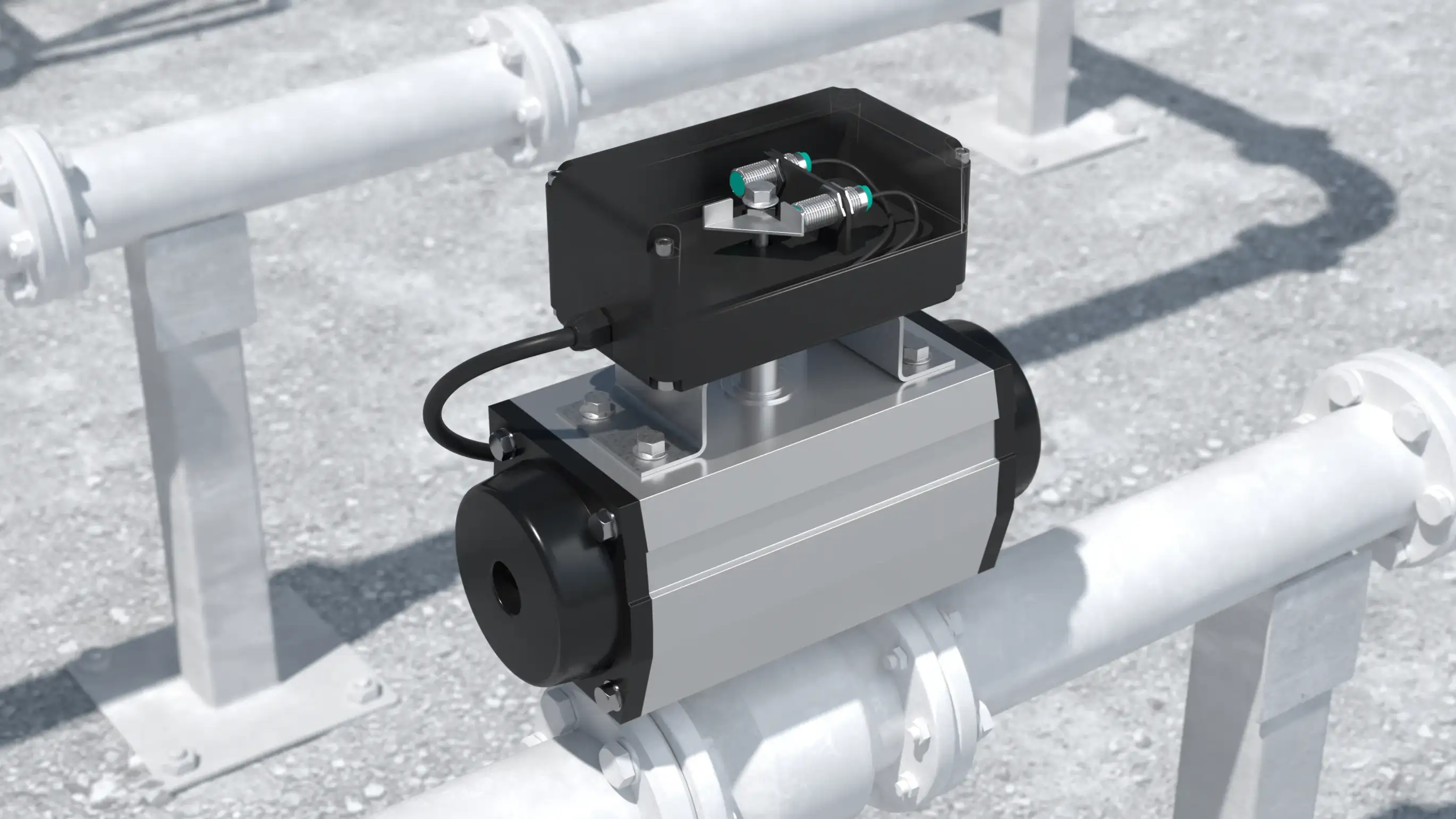
The Goal
Process control requires reliable real-time information about the closing position of the valve. Exact recording of the closing processes should also provide analysis data that reflects the wear condition of the device, allowing components to be replaced in a timely manner as part of predictive maintenance. Precise and condition-based planning of maintenance work is intended to minimize downtimes while maximizing maintenance efficiency.
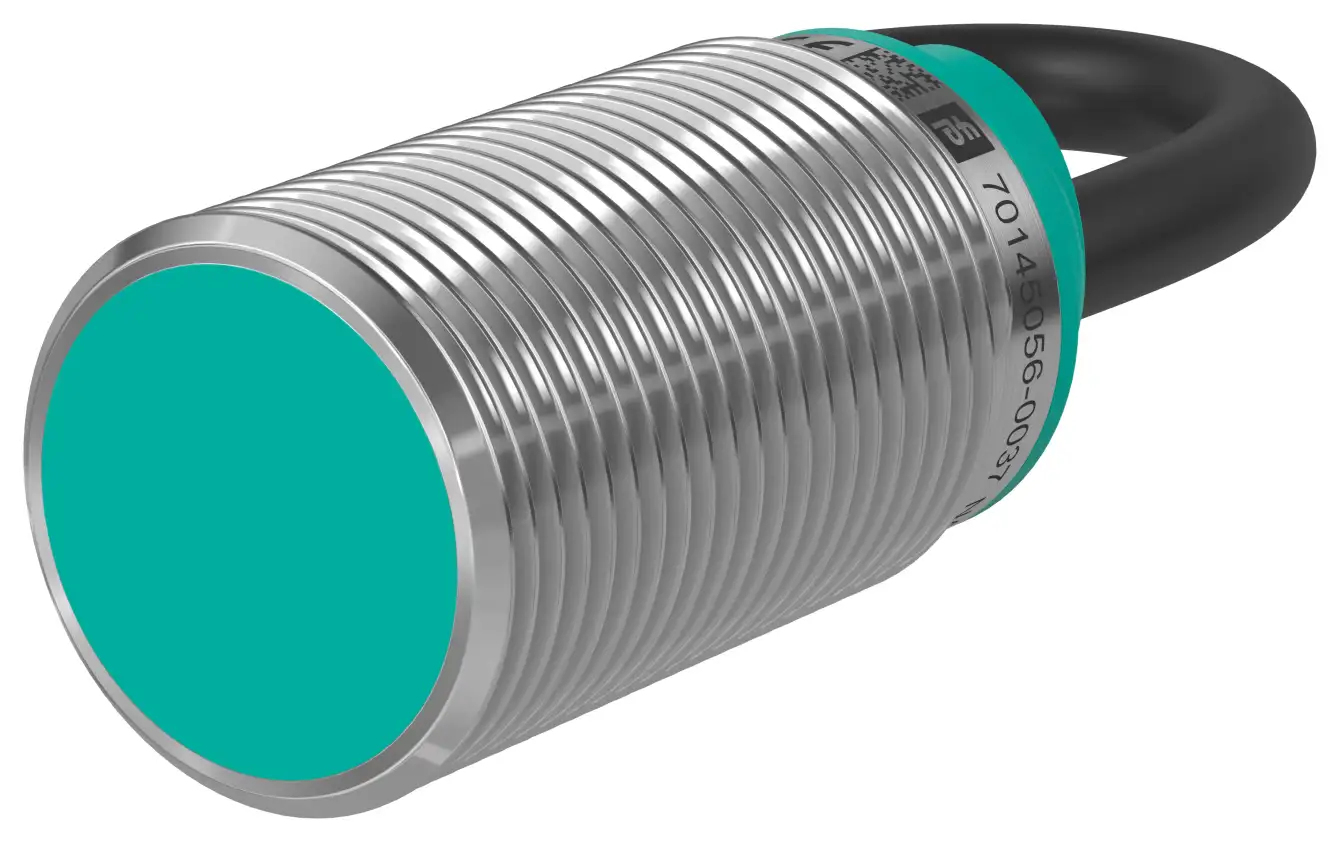
The Solution
The end positions of the valve are detected by two inductive distance sensors. These also measure the speed and acceleration of the positioning process, even at very high object speeds (up to 3 m/s). The data from the distance, speed, and acceleration measurements is transmitted via the integrated IO-Link interface. This provides insight into the level of contamination and wear on the valve, forming the basis for condition monitoring and predictive maintenance.
Two measuring windows can be configured on the sensor in order to obtain a precise acceleration value for differentiated sequence monitoring. If the opening and closing movement exceeds defined limit values, needs-based maintenance is triggered. Compared to purely time-based cyclical maintenance, this saves personnel and costs.
Technical Features
■ Robust noncontact measuring principle
■ Maximum switching distance up to 30 mm
■ Target speed up to 3 m/sec
■ Switching frequency up to 1,400 Hz
■ IO-Link interface
■ Various housing designs
■ Integrated temperature sensors (optional)
The Advantages
Based on the historical data, maintenance processes can be planned for the long term and integrated into the operating process, avoiding unplanned system downtimes. The resulting increase in plant efficiency can lead to considerable cost savings. In addition, a consistently good maintenance condition of the valves contributes to a smooth process and the protection of other system components.
At a Glance
- Inductive distance sensors determine switch points,speed, and acceleration
- Precise measurement even at very high target speeds
- Additional comprehensive data and parameterizable limit values for temperature, operating times, and counters
- IO-Link interface transmits detailed information for condition monitoring and predictive maintenance