Monitoring Strip Position and Ejection in a 9-Station Die
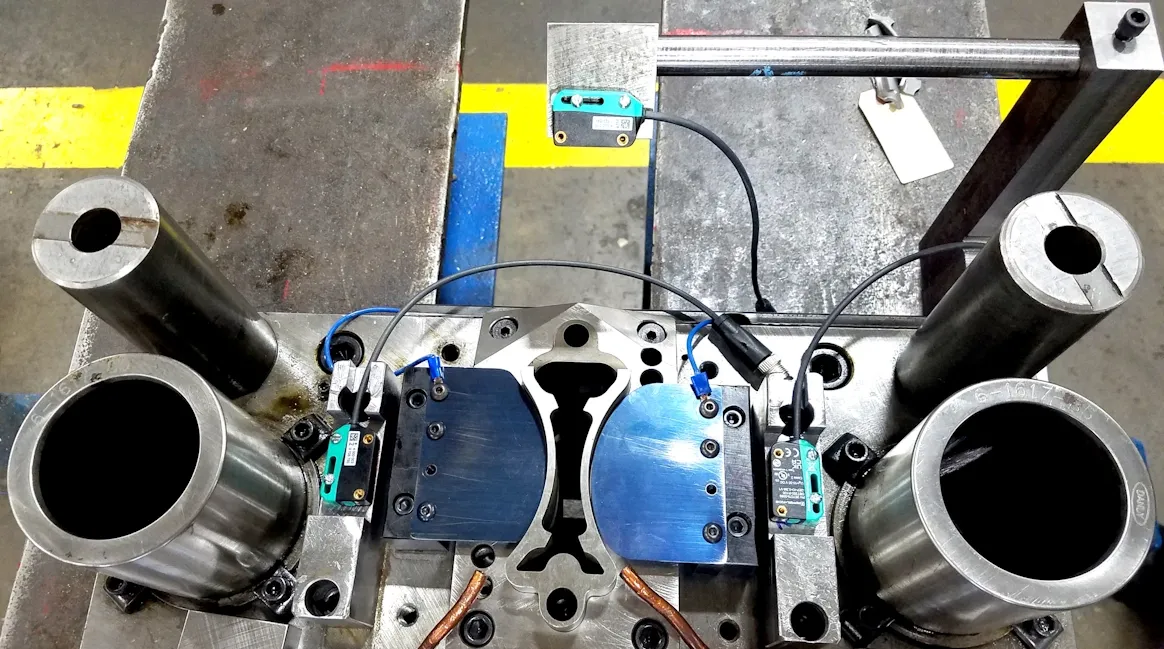
BGS Sensors Reliably Control Feed Stop and Verify Part Ejection
The Application
Die makers at a privately owned Tier 2 metal forming company that manufactures products for a wide variety of industries, including automotive, were recently tasked with developing a nine-station progressive die to produce metal brackets for a car suspension assembly. At the strip’s final station, the finished left and right parts are cut off the main strip and pneumatically ejected via a chute into a collection bin.
The Goal
The objective of the in-die sensor solution is twofold: Firstly, the customer wants to ensure that the part (strip) is positioned correctly for the final cut. If there is an overfeed or underfeed, the cut will be made in the wrong location, resulting in bad parts. Secondly, once the part has been cut, it is to be confirmed that a jet of compressed air has successfully removed all parts from the die before the next downstroke. If a finished part remains in the press, the next downstroke could cause a very expensive die crash.
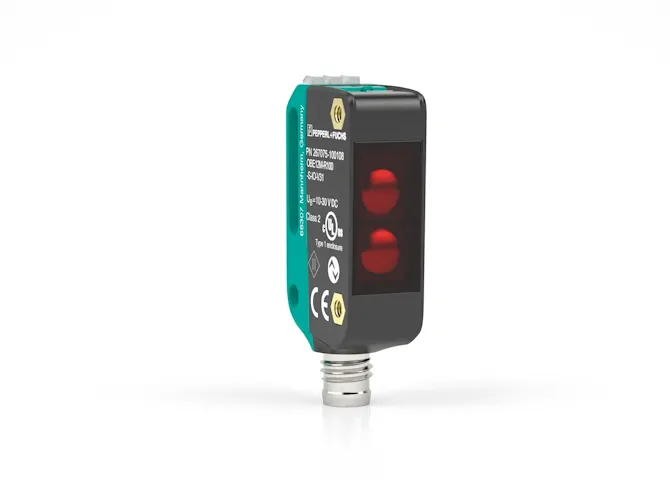
The Solution
To solve the positioning application, the customer placed a photoelectric triangulation sensor with background suppression (BGS) (OBT350-R100-2EP-IO-0,3M-V1) outside the die, aimed precisely at the point where the feed must stop.
To verify whether the parts were ejected, two more sensors of the same model were mounted on opposite sides of the cutting station and set to ignore the metal background—the shoulder on which the part rests. If the part ejection was unsuccessful, the sensors alert the controller that a part either remains on the shoulder or lies on the plate beneath it. The sensor features 256 receiver pixels and a custom evaluation algorithm that provides laser precision while offering the motion forgiveness required in many end-of-feed applications.
Technical Features
- Miniature design with versatile mounting options
- Best background suppression in its class
- Precision object detection, virtually independent of color
- Extended temperature range: -40 °C ... +60 °C
- High degree of protection (IP69K)
- IO-Link interface for service and process data
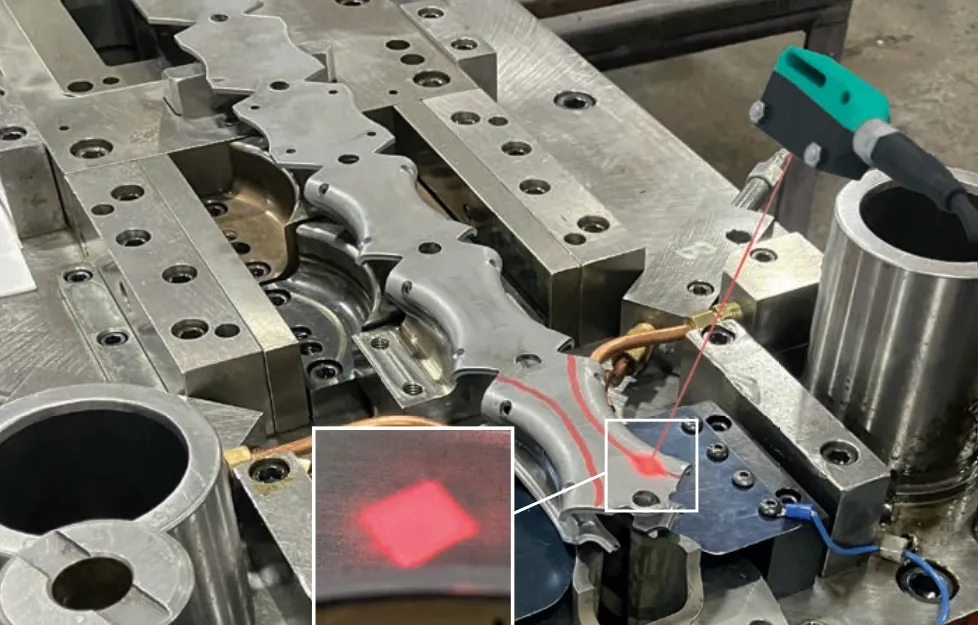
The Benefits
The customer had initially tried a laser-based solution from a competitor, which had a very precise (tiny) light spot that caused an unstable output when the target metal vibrated or bent. In contrast, the 5 mm x 5 mm wide evaluation light beam of the OBT350 provides reliable strip detection at the end-of-feed point. The background suppression sensor only detects the part and not the metal background or surroundings. It is also insensitive to color changes and detects variations in shine or metal discoloration without compromising the sensor accuracy. The OBT350 triangulation sensor with background suppression and multipixel array technology ultimately fulfills all key application criteria.